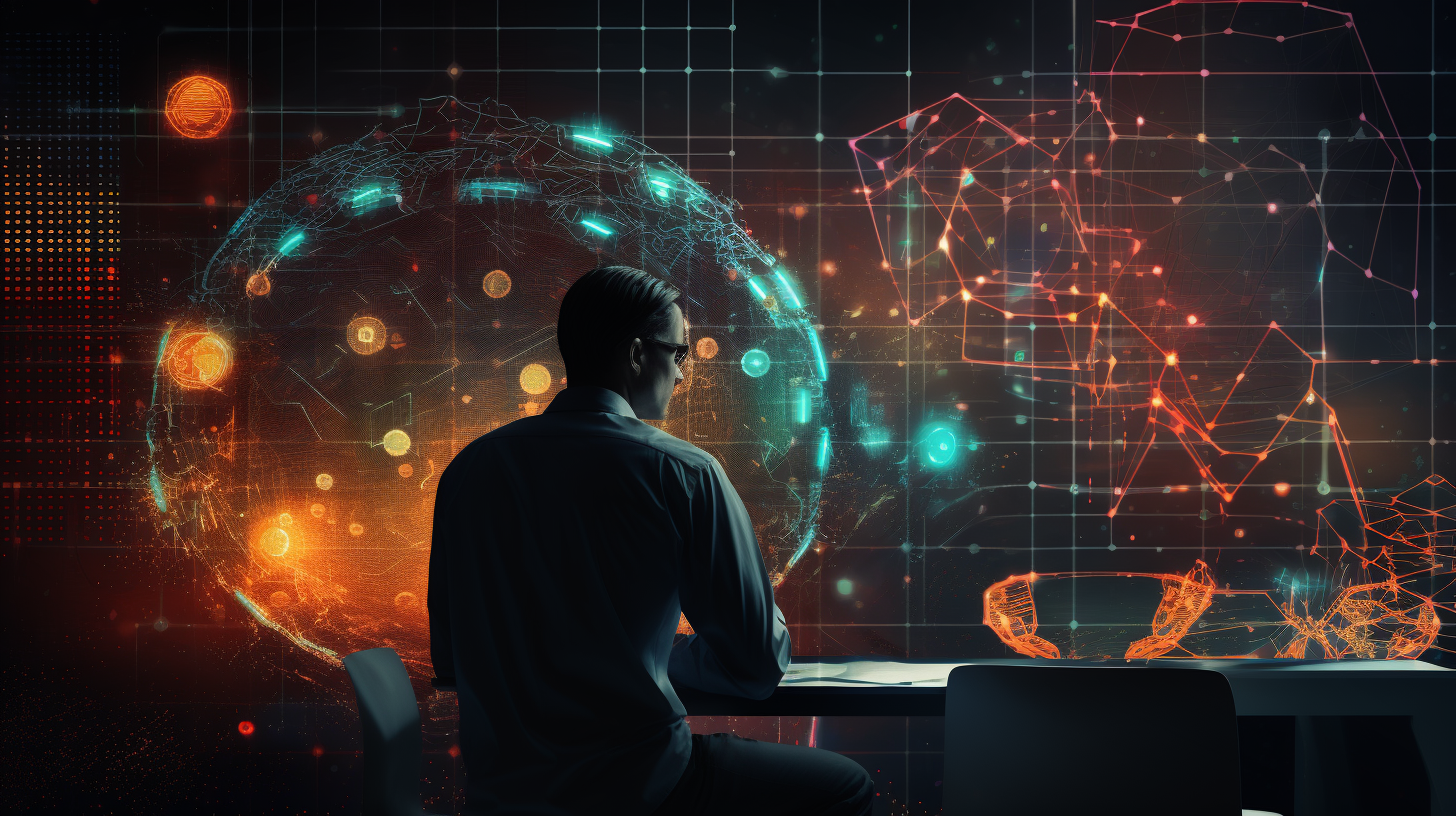
Florida Lean Six Sigma Problem Solving with AI ChatGPT and Organizational Change Leadership
Florida Lean Six Sigma Master Black Belt, mentored by six sigma co-creator Dr. Mikel Harry, Deming disciple Dr. Yoshida and plant director Jesse Wingard of NUMMI GM-Toyota joint venture, combines ChatGPT, AI powered RPA, machine learning, and org change leadership to pioneer the next generation of continual improvement and digital transformation.
By Frank Shines
March 14, 2023
As a Florida Lean Six Sigma Master Black Belt and Digital Transformation expert, I have had the privilege of working on dozens of national and global process improvement and digitization projects with some of the most fascinating people. I have been blessed to travel the world on someone else’s dime working on all sorts of challenging and interesting business problems with many of the Fortune 500 companies and Global 2000 corporations. One of the key problem-solving methodologies that I’ve used is Lean Six Sigma, which has a long history dating back to pre-World War II. Over the years, I have learned that by combining Lean Six Sigma with Organizational Change Leadership, Quality Management Systems and Artificial Intelligence / Machine Learning (AIML), I have been able to achieve the best results for my clients and for our family businesses.
Unfortunately, it was under tragic circumstances that a Florida Lean Six Sigma connection led to my career choice as a management and technology consultant. In January of 1986, I was a cadet at the U.S. Air Force Academy in Colorado Springs. The entire cadet wing was excited to watch the upcoming launch of the Space Shuttle Challenger. I was particularly thrilled because my classmate’s father, Major Dick Scobee, would be the commander of this flight. On January 28, the Space Shuttle Challenger departed from Cape Canaveral Florida. But 73 seconds after liftoff something went terribly wrong. There was a catastrophic explosion and all seven crew members perished. The Air Force Academy was asked to assist with some of the investigation along with the renowned physicist Dr Richard Feynman. That is when I learned how the power of statistics and Lean Six Sigma could save lives.
In the 1920s and 1930s, Dr. Walter Shewhart and Dr. W. Edwards Deming were working at Bell Labs in New Jersey, where they developed the Statistical Process Control (SPC) chart. This chart helped engineers and managers to visualize data and understand whether a process was under control or not. In general, when a process is in a state of statistical control, it is predictable and working in a manner that minimizes errors, time and cost. That does not mean that it cannot be further improved. Lean Six Sigma is forever seeking perfection through a cycle of continual improvement, call the PDCA cycle (Plan-Do-Check-Act, repeat). Dr. Deming later took this knowledge to Japan, where he taught the principles of SPC and quality control to Japanese engineers and government and business leaders.
After World War II, Japan experienced an economic boom, and companies like Toyota were eager to improve their processes and compete with the rest of the world. It was during this time that the principles of Lean Manufacturing evolved from the Toyota Production System (TPS), the brainchild of Taichi Ohno, of Toyota.
Lean principles are focused on eliminating waste in processes, while Six Sigma focuses on reducing defects and variability. Together, they form a powerful approach for improving processes and driving continuous improvement.
One of the key figures in the development of Six Sigma was Dr. Mikel J Harry, who along with Bill Smit working under the directive of Motorola CEO Bob Galvin co-created Six Sigma with Motorola in the 1980s. Harry was also instrumental in the development of the Master Black Belt certification, which I had the honor of earning.
Since then, companies all over the world have embraced Lean Six Sigma and have seen significant improvements in their processes and bottom lines. Companies like Amazon and Tesla are applying the principles of Lean Six Sigma combined with automation and artificial intelligence to drive even more efficiency and innovation.
In my own work, I have led numerous Lean Six Sigma projects that have delivered significant benefits to my clients. For example, I reduced patient shipment errors and turnaround time by 47% and 32%, respectively, and cut medical device scrap by nearly 50%, while raising productivity over 36%. I have also helped to increase Net Promoter Score (NPS) by 11 points, cutting the cost of customer acquisition.
Looking to the future, I believe that Lean Six Sigma will continue to be a critical methodology for companies looking to improve their processes and stay competitive. As technology continues to advance, we will see even more opportunities to combine Lean Six Sigma with automation and artificial intelligence to drive even greater improvements in efficiency, productivity, and innovation.